„Menschen machen den Unterschied!“ – das weiß jeder Unternehmer. Aber auch: „Wir müssen mit dem arbeiten, was wir haben.“ Und genau da kommt es immer wieder zu Diskussionspunkten. Denn häufig fragen sich bestehende Mitarbeiter, was ihre Rolle in der Transformation hin zur digitalen Fertigung ist.
Inhaltsverzeichnis: Das erwartet Sie im Artikel
Digitale Fabrik: Ein Überblick über das Konzept und seine Bedeutung
Es gibt viele Definitionen des Buzzwords „Digitale Fabrik“. Dieser Beitrag stützt sich auf die Definition des VDI. Also: Eine Vernetzung der gesamten Produktionsstätte durch digitale Modelle und Methoden. Das Ziel ist es, diese Fabrik digital zu planen, in der Realität umzusetzen, sie zu steuern und überwachen sowie laufende Verbesserungen vorzunehmen.
Integration der Funktionen im Projektmanagement: Von der Planung bis zur Umsetzung
Sämtliche Funktionen des Unternehmens ergänzen ihre Perspektive auf ein Projekt. Daher spielen sie bereits in der Planung, aber auch in späteren Phasen des Projekts eine Rolle mit wechselnder Wichtigkeit.
So gibt beispielsweise der Vertrieb den Anstoß für eine Entwicklung. Die entsprechende Abteilung entwickelt gemeinsam mit den Kollegen aus Produktion und Einkauf ein Produkt weiter.
Das Controlling überprüft die finanzielle Machbarkeit, während der Vertrieb abgleicht, ob das entwickelte Produkt den Kundenwünschen entspricht.
Vorteile der digitalen Fabrik: Kostenreduktion, Flexibilität und Qualitätssteigerung durch virtuelle Planung
Die digitale Fabrik verspricht als Weiterentwicklung der herkömmlichen Fabriken eine Steigerung der Effizienz und Produktivität, da digital alle Szenarien analysiert wurden und die meisten Fehlerquellen bereits im Vorfeld eliminiert wurden.
Dadurch sinken die Kosten, denn das Planungsstadium nimmt deutlich weniger Ressourcen in Anspruch: Da die meisten oder alle Schritte virtuell stattfinden, kommen Prototypen beispielsweise nicht mehr zum Einsatz. Ihre physischen Eigenschaften wurden virtuell simuliert und dem Projekt entsprechend perfektioniert.
Die Flexibilität steigt, denn neue und weiterentwickelte Produkte erlangen schneller die Marktreife. Dies geschieht nicht zuletzt aufgrund von ständigen Verbesserungen, die ihre Effekte zum Teil im laufenden Betrieb ausspielen. Zudem stehen gewonnene Erkenntnisse in folgenden Projekten zur Verfügung.
Idealerweise steigt die Qualität der Produkte durch die kontinuierlichen Verbesserungen am Prozess. Da Daten von vielen Quellen in Echtzeit zur Verfügung stehen, verbessern sich die darauf basierenden Entscheidungen. Ein Beispiel: Die Temperatur eines Anlagenteil erhöht sich langsam. Während das Wartungsteam vorsorglich die Anlage überprüft, steht die Produktion. Diese Maßnahme verhinderte einen Defekt der Maschine, der einen teuren Produktionsausfall nach sich gezogen hätte.
Zusätzlich steigt die Nachhaltigkeit der gesamten Produktionskette. Denn es werden weniger Ressourcen eingesetzt, wie physische Werkstoffe für den Prototyp oder Energie, um diese zu bearbeiten.
Digitale Fabrik: Was ist bereits realisiert?
ruhlasmart beispielsweise setzt unter anderem auf die Entwicklung von „Digital Twins“, um im Vorhinein Anlagen testen zu können.
In diesem Schritt zeigen sich erste Schwachstellen, die dann ausgebessert werden. Zusätzliche Berechnungen ergeben, wann der jeweilige Teil der Anlage gewartet werden muss.
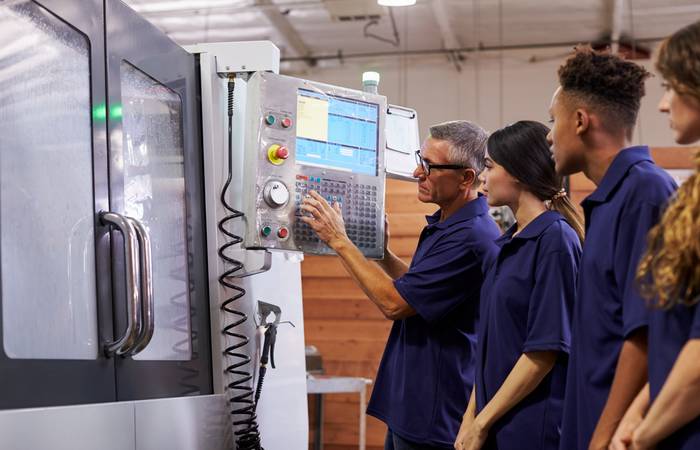
Daher setzen viele Unternehmen auf einen Mittelweg: Das gegenwärtige Team entwickelt neue Kompetenzen durch klassische Weiterbildung. (Foto: AdobeStock - 129569547 Monkey Business)
Neben weiteren datenbasierten Produkten bietet das Unternehmen Schulungen an. Diese ermöglichen es den Mitarbeitern, die Technologien effizient einzusetzen.
Mitarbeiter und die digitale Fabrik
Technologien spielen eine immer wichtigere Rolle. Jedoch sind sie nur so stark, wie die Persönlichkeit, die mit ihr umgeht. Nur weil es beispielsweise jemand versteht, die Daten der Maschine sinnvoll mit den Daten aus dem Einkauf zu verknüpfen, kann diese Person sie interpretieren.
Es gilt herauszufinden, welche individuellen Fähigkeiten die Mitarbeiter haben. Daher ist es besonders wichtig, alle Mitarbeiter auf den Weg zur digitalen Fabrik einzubinden. Das Management gleicht diese Fähigkeiten mit den Anfordernissen des jeweiligen Projekts ab. Ergebnis dieser Analyse kann sein, dass die gegenwärtigen Fähigkeiten weiterentwickelt und ergänzt werden müssen.
Der Status Quo
Zeitgleich mit der digitalen Fabrik entwickeln sich neuartige Berufe. Ein Beispiel sind Industrielle Datenanalysten. Ihre Aufgabe ist es, die vielseitigen Daten aus verschiedensten Quellen zu extrahieren: Von den Maschinen selbst, aber auch aus dem Einkauf, dem Lager bis hin zu den Kunden.
Im nächsten Schritt analysieren sie diese Daten und verwenden die Ergebnisse, um die Produktionsanlage und ihre Ergebnisse zu steuern und zu verbessern.
Zahlreiche weitere Berufe entstehen im Umfeld der digitalen Fabrik, besonders in den Bereichen der Digitalisierung, der IT und des IIoT – des Industrial Internet of Things.
Die rasante Weiterentwicklung der digitalen Fabrik macht jedoch auch Angst: Vielen älteren Arbeitnehmern fallen Veränderungen nicht leicht. Sie befürchten – in manchen Fällen zurecht, dass ihre Tätigkeit als Dreher, Schlosser oder Werkzeugbauer wegfallen könnte.
Auch in verwaltenden Berufen entstehen ständig neue Themen, so werden beispielsweise neue Softwares verwendet. Mitarbeiter müssen die damit zusammenhängenden Prozesse erstmal verstehen, bevor sie effektiv eingesetzt werden können.
Abgesehen davon verfügen gerade erfahrene Mitarbeiter über Detailwissen, dass in keinem Lehrbuch steht. Wenn alle Beteiligten ergebnisoffen nachdenken, können sie Wege und Werkzeuge finden, um sie in das Netz der digitalen Fabrik einzubinden.
Mitarbeiter auf dem Weg zur digitalen Fabrik: Entscheidung gefragt
Die Veränderung hin zur digitalen Fabrik erfordert den Einsatz neuer Fähigkeiten. Menschlicher Fähigkeiten. Nun steht jeder Unternehmer vor der Entscheidung, diese Fähigkeiten einzukaufen oder unternehmensintern auszubilden. In Zeiten vom Fachkräftemangel können beide Wege teuer und langwierig sein.
Daher setzen viele Unternehmen auf einen Mittelweg: Das gegenwärtige Team entwickelt neue Kompetenzen durch klassische Weiterbildung. Ein Beispiel wären Inhouse-Seminare des Entwicklungsteams zum Einsatz einer neuen Software. Oder einzelne Mitarbeiter studieren berufsbegleitend. Zeitgleich ergänzen neue Mitarbeiter mit gefragten Kompetenzen die bereits vorhandenen Fähigkeiten. So entstehen hochqualifizierte Arbeitsplätze, die auf lange Sicht erhalten bleiben.
Mitarbeiter in der Produktion bekommen durch die Entwicklung zur digitalen Fabrik andere Werkzeuge, die ihre Fähigkeiten ergänzen. So ermöglicht ein Exo-Skelett beispielsweise das physische Bearbeiten von hochgewichtigen Werkstücken – die körperliche Kraft des individuellen Mitarbeiters ist jetzt nicht mehr wichtig. In dieser Situation kann die erfahrene Persönlichkeit ihre vorhandenen Kenntnisse länger einbringen – und an jüngere Kollegen weitergeben.
Zugleich bedeutet das für alle Unternehmensangehörigen, dass sie sich zeitgleich zur Entwicklung der digitalen Fabrik im jeweiligen Bereich entwickeln müssen.
Fazit: Menschen sind wichtig
Dieser Beitrag hat gezeigt, wie eine wahre digitale Fabrik – also die Vernetzung aller Ressourcen, sei es Mensch oder Maschine, entsteht: Essenziell dazu sind Mitarbeiter mit den richtigen Fähigkeiten. Zeitgleich ist das Management gefordert, diese in Abgleich mit den jeweiligen Anforderungen zu bringen. Dazu kann es erforderlich sein, einzelne Fähigkeiten erst zu entwickeln.
So wie die digitale Fabrik idealerweise auf Daten aus allen Unternehmensbereichen, wie dem Einkauf, dem Lager, dem Vertrieb und der Produktion zurückgreift, gilt es Mitarbeiter mit Kompetenzen in diesen Bereichen an der Planung zu beteiligen. Erst dann können versierte Mitarbeiter die Planung digital umsetzen, bevor in einem dritten Schritt das Projekt physisch realisiert wird. Jetzt ändert sich die Funktion der Planer: Sie sehen nun, welche Schritte in der Realität verbessert werden können.